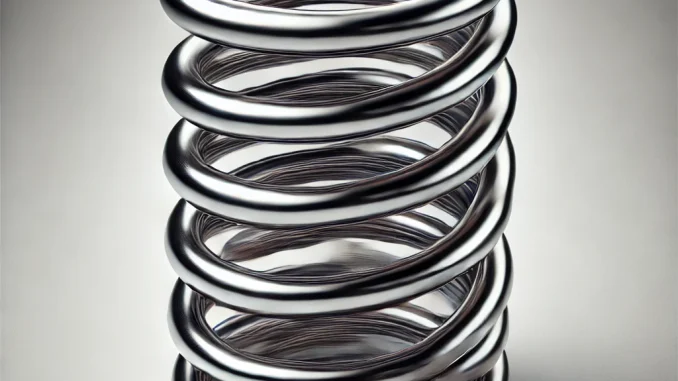
Stahlfedern spielen eine unverzichtbare Rolle in zahlreichen mechanischen Anwendungen, von der Automobilindustrie bis hin zur Luft- und Raumfahrttechnik. Ihre Funktionalität und Leistungsfähigkeit hängen von einer Vielzahl von Faktoren ab, die bei der Auswahl sorgfältig berücksichtigt werden müssen. Dieser Artikel gibt Ihnen detaillierte Einblicke und wertvolle Tipps, um die geeigneten Stahlfedern für Ihre spezifischen Anforderungen auszuwählen.
Materialwahl und Eigenschaften
Die Wahl des geeigneten Werkstoffs ist ein entscheidender erster Schritt bei der Auswahl von Stahlfedern. Unterschiedliche Stahlsorten bieten verschiedene mechanische Eigenschaften, die sich direkt auf die Leistungsfähigkeit der Feder auswirken. Chrom-Vanadium-Stähle beispielsweise zeichnen sich durch hohe Zugfestigkeit und Elastizität aus, was sie ideal für stark beanspruchte Anwendungen macht. Rostfreie Stähle bieten hingegen eine ausgezeichnete Korrosionsbeständigkeit, weshalb sie bevorzugt in Umgebungen mit hoher Feuchtigkeit oder aggressiven Chemikalien eingesetzt werden.
Federkraft und Spannungsverteilung
Ein zentrales Kriterium bei der Auswahl von Stahlfedern ist die Federkraft, die maßgeblich von der Materialstärke, dem Durchmesser und der Windungszahl abhängt. Federn müssen so konzipiert sein, dass sie die benötigte Kraft ohne bleibende Verformung liefern können. Eine sorgfältige Berechnung der Spannungsverteilung innerhalb der Feder ist unerlässlich, um sicherzustellen, dass die Belastungsgrenzen des Materials nicht überschritten werden. Finite-Elemente-Methoden (FEM) sind hier ein nützliches Werkzeug, um die Spannungen präzise zu analysieren und das Design zu optimieren.
Ermüdungsfestigkeit und Lebensdauer
Die Ermüdungsfestigkeit von Stahlfedern ist ein weiterer kritischer Aspekt, der bei der Auswahl berücksichtigt werden muss. Federn unterliegen oft zyklischen Belastungen, die im Laufe der Zeit zu Materialermüdung und letztlich zum Versagen führen können. Eine hohe Ermüdungsfestigkeit gewährleistet eine längere Lebensdauer und erhöhte Zuverlässigkeit der Feder. Hier spielen sowohl die Materialwahl als auch die Oberflächenbehandlung eine Rolle. Verfahren wie Kugelstrahlen können die Oberflächenhärte verbessern und somit die Ermüdungsfestigkeit erhöhen.
Geometrie und Designoptimierung
Die geometrische Gestaltung einer Feder hat einen direkten Einfluss auf ihre Leistungsfähigkeit und Lebensdauer. Die Wahl zwischen Druck-, Zug- oder Torsionsfedern hängt von der spezifischen Anwendung ab.
Druckfedern sind beispielsweise ideal für Anwendungen, bei denen Kräfte in einer geraden Linie wirken, während Zugfedern für Anwendungen geeignet sind, bei denen die Feder durch Zugkräfte belastet wird. Torsionsfedern kommen zum Einsatz, wenn Drehmomente übertragen werden müssen. Die genaue Berechnung der Windungszahl, des Drahtdurchmessers und der Federlänge ist entscheidend für eine optimale Leistungsfähigkeit.
Temperaturbeständigkeit
In vielen Anwendungen müssen Stahlfedern extremen Temperaturen standhalten. Hochtemperaturstähle oder spezielle Legierungen sind notwendig, um die mechanischen Eigenschaften bei hohen Temperaturen aufrechtzuerhalten. Bei tiefen Temperaturen müssen Materialien ausgewählt werden, die ihre Zähigkeit und Flexibilität beibehalten. Die Temperaturbeständigkeit der Feder beeinflusst nicht nur ihre unmittelbare Leistung, sondern auch ihre langfristige Zuverlässigkeit und Lebensdauer.
Korrosionsbeständigkeit
In korrosiven Umgebungen ist die Korrosionsbeständigkeit der Stahlfedern von entscheidender Bedeutung. Der Einsatz von rostfreien Stählen oder speziellen Beschichtungen kann die Lebensdauer der Federn erheblich verlängern. Galvanische Beschichtungen, Passivierung oder die Verwendung von Korrosionsschutzmitteln sind gängige Methoden, um die Widerstandsfähigkeit gegen Korrosion zu erhöhen. In besonders aggressiven Umgebungen kann der Einsatz von Kunststoffbeschichtungen eine zusätzliche Schutzschicht bieten.
Qualitätsprüfung und Zertifizierung
Die Qualitätsprüfung und Zertifizierung sind wesentliche Schritte, um sicherzustellen, dass die ausgewählten Stahlfedern den erforderlichen Spezifikationen entsprechen. Industriestandards wie ISO 9001 oder spezielle Normen für die Automobil- oder Luftfahrtindustrie geben klare Richtlinien vor. Durch zerstörungsfreie Prüfverfahren (NDT) wie Ultraschall- oder Röntgeninspektionen kann die Integrität der Federn überprüft werden, ohne sie zu beschädigen. Regelmäßige Qualitätskontrollen während der Produktion gewährleisten, dass jede Feder den hohen Anforderungen gerecht wird.
Anwendungsbeispiele und Branchenlösungen
Die Anwendungsmöglichkeiten von Stahlfedern sind vielfältig. In der Automobilindustrie werden sie in Fahrwerksystemen, Kupplungen und Motorventilen eingesetzt. In der Luft- und Raumfahrt finden sie Verwendung in Landefahrwerken, Steuerungssystemen und Schubdüsen.
Jede Branche hat spezifische Anforderungen an die Federn, die oft maßgeschneiderte Lösungen erfordern. Die Zusammenarbeit mit erfahrenen Herstellern, wie etwa Alcomex, und die Nutzung von Simulationssoftware können helfen, die ideale Feder für die jeweilige Anwendung zu entwickeln.